
BELT FEEDERS

Benefits and Features
​
Belt feeders are a very common type of large capacity feeder used in mining and heavy industry. When designed correctly, they are a cost effective and reliable solution for feeding a range of materials - from large lumps to cohesive filter cakes.
Options and features typically include the following:
​
-
Range of belt cover options including FRAS, Oil Resistant, High Temperature, and Wear Resistant
-
Belt widths up to 2.4m
-
Fabric weave or steel cord belting options to suit required tensions
-
Ceramic or standard diamond grooved rubber lagged pulleys
-
full length side skirts with adjustable wear resistant skirt plates and secondary dust skirt options
-
Instrumentation to detect belt drift, belt rips and belt slip
-
Primary and secondary belt cleaners, return belt ploughs and spray bar cleaning option
-
Guarding to Australian Standards AS4024.3610
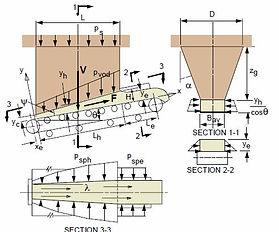

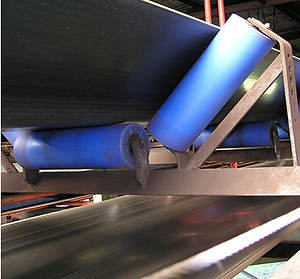
BELT FEEDERS FOR BULK MATERIALS
Our mechanical and structural engineers have decades of experience in the design and manufacture of custom belt feeders and hoppers to suit a wide range of materials and feed rates.
BHT Belt Feeders are designed and manufactured to ensure long life and reliable service in the harshest of operating environments. Using only proven, quality components, our designs meet or exceed Australian Standards and can include the design and supply of a complete system including hopper, structure, isolation gate and discharge conveyors as required.
By working with BHT for the supply of your next belt feeder you will enjoy the following benefits:
-
A tailored solution, engineered to suit the site specific application,
-
Compliance to customer engineering and manufacturing specifications,
-
A consultative design process utilising the latest industry standards and guidelines for material flow properties, Australian Standards and BHT proprietary design systems,
-
The confidence of Finite Element Analysis for major structural and mechanical components,
-
Provision of 3D models to allow convenient integration into overall plant layouts to ensure accurate interface and tie-in with connecting chutes and infrastructure.
​
DESIGN FOCUS
CONVEYOR BELTING
A characteristic of belt feeders is that all pull-out forces and frictional resistances are transferred directly through tension in the belt to the drive pulley. Consequently, selection of the belt is critical to the performance and life of any belt feeder. It should be noted however that belt stiffness increases with tensile strength and therefore the belt selection can have a significant impact on pulley diameters. This in turn can significantly affect the gearbox size and torque requirement for the drive.
Correct determination of belt tensions is therefore extremely important - under specifying pull-out forces can lead to over-stressed components or even complete failure, while over specifying can lead to unnecessary expense. Correct design of the hopper : feeder system using reliable and representative flow property data is paramount. With correct flow property data, critical hopper geometry can be determined and changes to hopper size and geometry can be investigated to optimise the belt tensions. Additionally, upgrading to a high friction lagging (such as ceramic) on the drive pulley increases the drive friction coefficient, minimising required take-up tensions and reducing the maximum belt tension.
​
In very high head load applications, steel cord belting becomes an option due to the high pull-out forces involved. Steel cord belt allows a smaller bend radius when compared to an equivalent high tension fabric belt. However, steel cord belting can get expensive and can often only be purchased in minimum lengths that are many times longer than required for a single belt feeder.
​
Therefore, in high tension applications, it is often preferable to consider an Apron Feeder or a hybrid Apron Belt Feeder solution. These feeders utilise chain as the main tension member, allowing smaller diameter sprockets at the terminal ends when compared to a belt pulley designed for high belt tensions.
The typical safety factors of fabric belts on maximum continuous operating tensions are 10:1 while steel corded belts are 6.7:1.
​
See the photo on left.
CONVEYOR IDLERS
Idlers provide belt support under the hopper and also along the extension or conveying zone. Idler assemblies incorporate rollers with rolling element bearings, minimising 'drag' and keeping belt tensions and power as low as possible.
As well as supporting the belt, the idler frame assembly develops the required 'troughing' of the belt to suit the application. On a belt conveyor, carry idler frames are typically installed as 3-Roll assemblies, with 35 or 45 degree 'wing' rollers to maximise carrying capacity. Due to the higher tensions and shorter span between pulleys on belt feeders, idler sets on belt feeders often have rollers arranged to create a long flat centre support, with short 20 degree 'picking' wing rollers to help contain product which escapes under the skirting.
​
Selecting the correct idlers for an application needs to consider the supported load, expected impact loads and rotational speed, and should also take account of material properties, maintainability and commonality of spares if a site has multiple machines.
On belt feeders, it is often required to install specially designed impact rollers in the feed zone. Impact rollers typically have rubber lagging or discs which help absorb impact forces generated when material is loaded on to the belt from height. These idlers often require larger shafts and bearings to cater for the expected loads. Depending on the application, impact beds can also be considered. These typically consist of impact bars with a low friction surface, allowing the belt to slide. Consideration must be given to the increase in belt tensions and also the generation of heat due to sliding impact beds.
To improve maintainability, particularly on larger belt feeders, idlers can be mounted on retractable support frames. This allows maintenance personnel to slide the idler assembly out into the maintenance corridor for easier replacement, rather than risking injury by reaching under the belt and lifting the heavy frame out in and awkward position.